1. वर्कपीस की संरचनात्मक विशेषताएं
वर्कपीस का आकार पतली दीवार वाला हैपहिये का वजनपंखे के आकार का है, सामग्री QT600 है, कठोरता 187-255 HBW है, अंदर एक विशेष आकार का छेद है, और सबसे पतला हिस्सा केवल 4 मिमी मोटा है। बैलेंस ब्लॉक की आयामी सटीकता आवश्यकताओं को चित्र 1 में दिखाया गया है। केंद्र छेद बी बेंचमार्क का व्यास Φ69.914-69.944 मिमी है, और सहिष्णुता केवल 0.03 मिमी है। नीचे एक प्रोफाइल वाला खाली छेद है। सी संदर्भ छेद और बाहरी सर्कल को मशीनिंग करते समय आंतरायिक कटिंग की जाती है। यहां दीवार की मोटाई केवल 4 मिमी है, जो काटने के तनाव और विरूपण को उत्पन्न करना और बी संदर्भ छेद के सहिष्णुता आकार को प्रभावित करना आसान है, जो वर्कपीस प्रसंस्करण में एक मुश्किल बिंदु है।
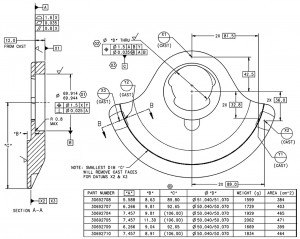
2. पारंपरिक शिल्प के छिपे हुए खतरे
मिलिंग प्रक्रिया के दौरान पतली दीवार वाले हिस्से आसानी से विकृत हो जाते हैं, मुख्य रूप से कटिंग स्ट्रेस और क्लैम्पिंग के कारण होने वाले विरूपण के कारण। पारंपरिक प्रसंस्करण योजना सीएनसी मशीनिंग केंद्र और सीएनसी खराद द्वारा संसाधित की जाती है, जिसे दो प्रक्रियाओं में विभाजित किया जाता है। एक है ओपी 10 प्रक्रिया। ऊपरी तल को ड्राइंग के आकार के अनुसार रफ और फिनिश करने के लिए Φ60 मिमी डिस्क मिलिंग कटर का उपयोग करें, आंतरिक छेद Φ51.04-51.07 मिमी से Φ50.7 मिमी (0.3-0.4 मिमी छोड़ें) को रफ मिल करने के लिए Φ20 मिमी मिश्र धातु मिलिंग कटर का उपयोग करें, आंतरिक छेद Φ69.914~69.944 मिमी से Φ69.6 मिमी (0.3~0.4 मिमी छोड़ें) को रफ मिलिंग करने के लिए Φ20 मिमी मिश्र धातु मिलिंग कटर का उपयोग करें, आंतरिक छेद Φ51.04~51.07 मिमी और Φ69.914~69.944 मिमी को बारीक बोरिंग कटर से बारीक बोरिंग करें, 2 ×Φ18 मिमी के दो छोटे छेदों को ड्रिल करें।
मशीनिंग की कठिनाईपहिये का वजन, संदर्भ छेद बी, ओपी 10 प्रक्रिया में ड्राइंग द्वारा आवश्यक आकार के लिए मशीनीकृत किया गया था। वर्कपीस को हटा दें और संदर्भ छेद बी, Φ69.914 ~ 69.944 मिमी के व्यास को मापें, और अंडाकार त्रुटि 0.005 ~ 0.015 मिमी है, और आकार ड्राइंग की आवश्यकताओं को पूरा करता है। हालांकि, ओपी 20 संसाधित होने के बाद, वर्कपीस को हटा दें और बी, Φ69.914-69.944 मिमी के संदर्भ छेद के व्यास को मापें, और अंडाकार त्रुटि 0.03-0.04 मिमी है। यह देखा जा सकता है कि व्यास ड्राइंग की आवश्यकताओं को पार कर गया है।
3. समाधान
टूलींग में सुधार करें। क्लैम्पिंग डिवाइस का डिज़ाइन सही है या नहीं, इसका सीधा असर वर्कपीस की मशीनिंग सटीकता सुनिश्चित करने, श्रम उत्पादकता में सुधार और श्रमिकों की श्रम तीव्रता को कम करने पर पड़ता है। पतली दीवार वाले भागों की विशेषताओं के कारण, अत्यधिक क्लैम्पिंग बल या असमान बल वर्कपीस के लोचदार विरूपण का कारण होगा, जो भाग के आकार और आकार सहिष्णुता की सटीकता को प्रभावित करेगा, और अंततः संसाधित भाग के आकार को सहनीयता से बाहर कर देगा। इस समस्या को हल करने के लिए, हाइड्रोलिक टूलींग को डिज़ाइन करते समय क्लैम्पिंग सिलेंडर और सपोर्ट सिलेंडर के मॉडल और आकार को सावधानी से चुना जाना चाहिए।
पोस्ट करने का समय: अगस्त-19-2022